Product Introduction
Polymer characterized by heat resistance, transparency, low moisture absorption, and solvent solubility
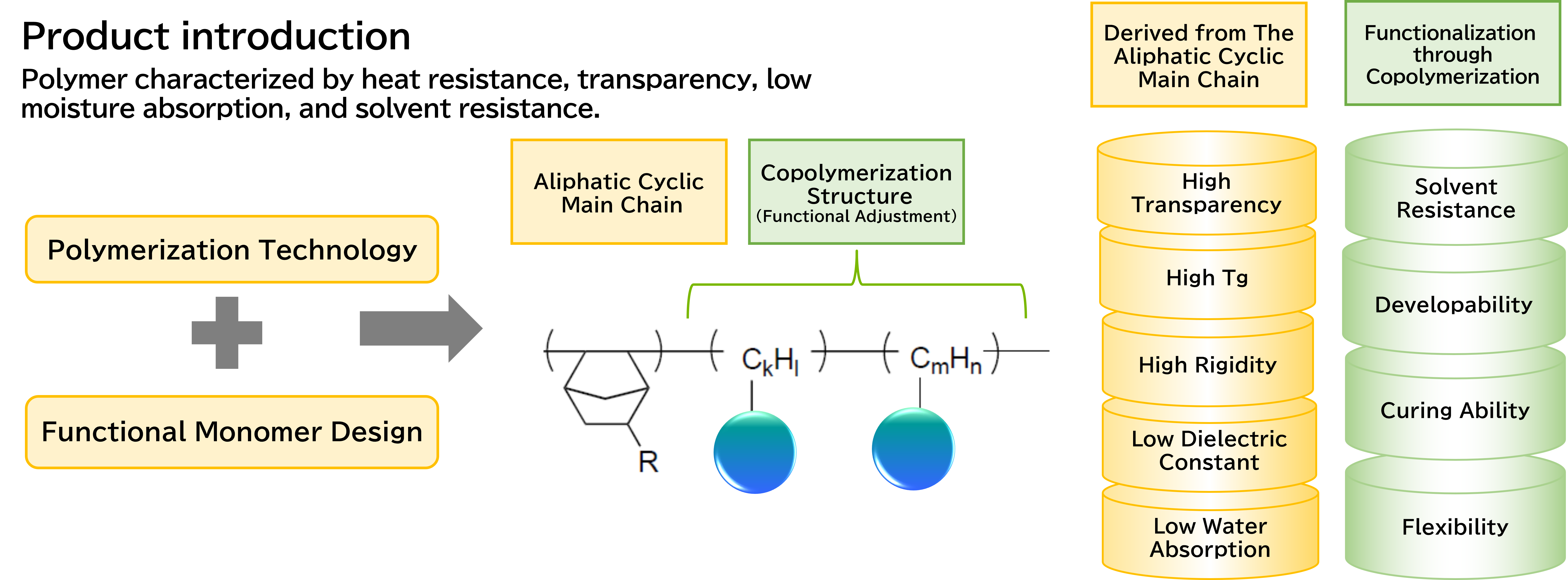
We develop functional polymers with a cyclic structure as the main backbone through polymerization techniques and functional monomer design.
The characteristics derived from the cyclic structure include high transparency, high Tg (glass transition temperature), high rigidity, low dielectric constant, and low water absorption.
By incorporating additional functionalities through copolymerization techniques, the resulting cyclic polymer exhibits unique properties such as solvent resistance, developability, curing ability through crosslinking groups, and flexibility.
Case Study
Contribution to Heat-resistant Materials
Post-acrylic Polymer
• Insufficient heat resistance with acrylic polymer.
Heat-resistant Optical Materials
• Achieving a balance between heat resistance and transparency.
Features
- • High Thermal Stability (High Tg)
- • Low Water Absorption
- • Excellent Light Transmittance
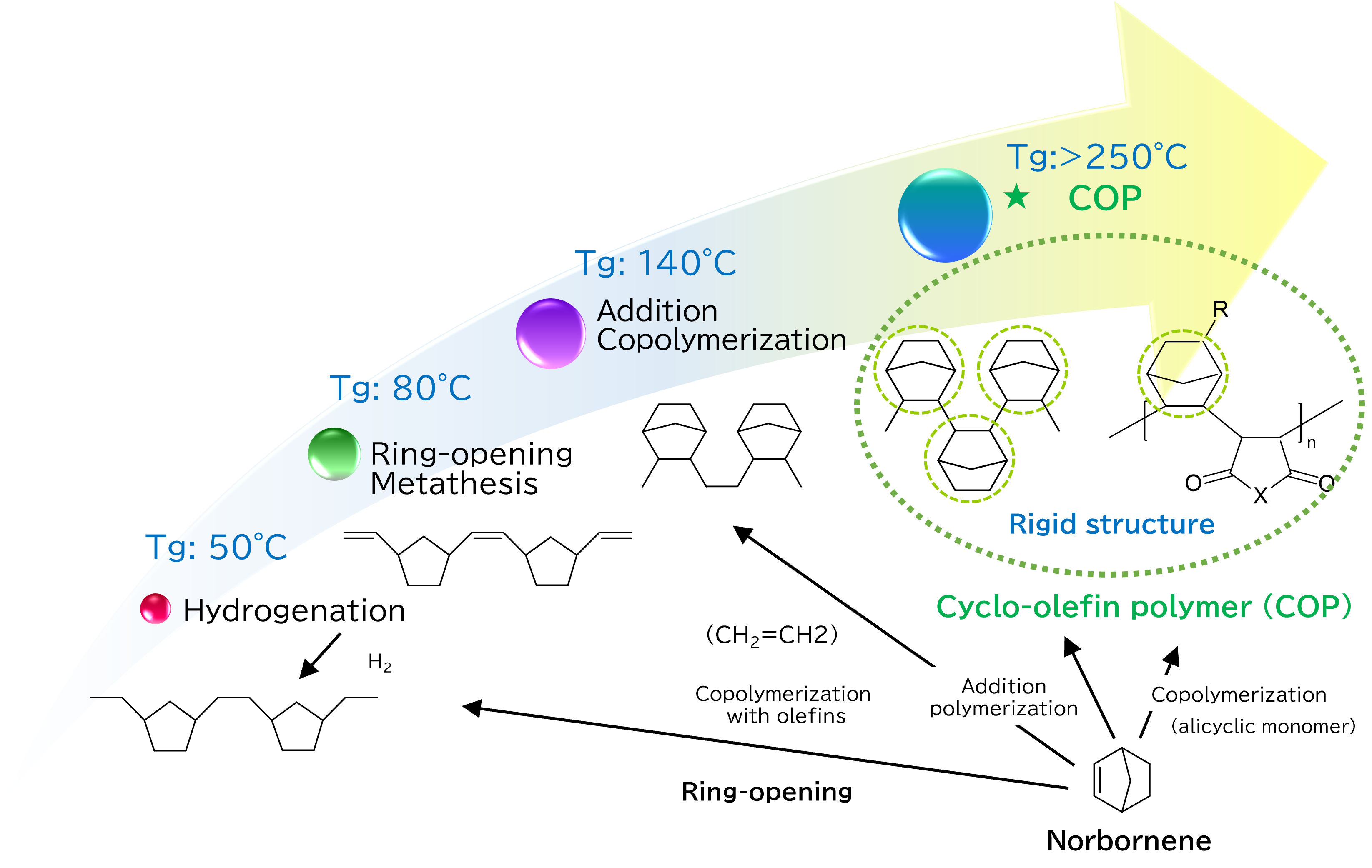
The properties derived from a cyclic backbone include high heat stability, low water absorption, and excellent light transmittance.
Addition polymers formed from cyclic monomers exhibit the superior characteristics of the cyclic backbone due to their rigid structure. They also demonstrate high heat resistance with a glass transition temperature (Tg) of 250 degrees Celsius or higher. Additionally, it is possible to control the Tg by copolymerizing with different monomers.
Applications
Examples of Intended Uses
- Semiconductor application
- Display devices (Display applications such as LEDs and organic LEDs)
- Sensor application
- Pharmaceuticals and food packaging materials
- Various coating applications
Can be deployed in various applications with distinctive functions.
The desired function can be obtained by designing the side chain functional group according to the application.
Example of use according to application (1)
Positive Photoresist
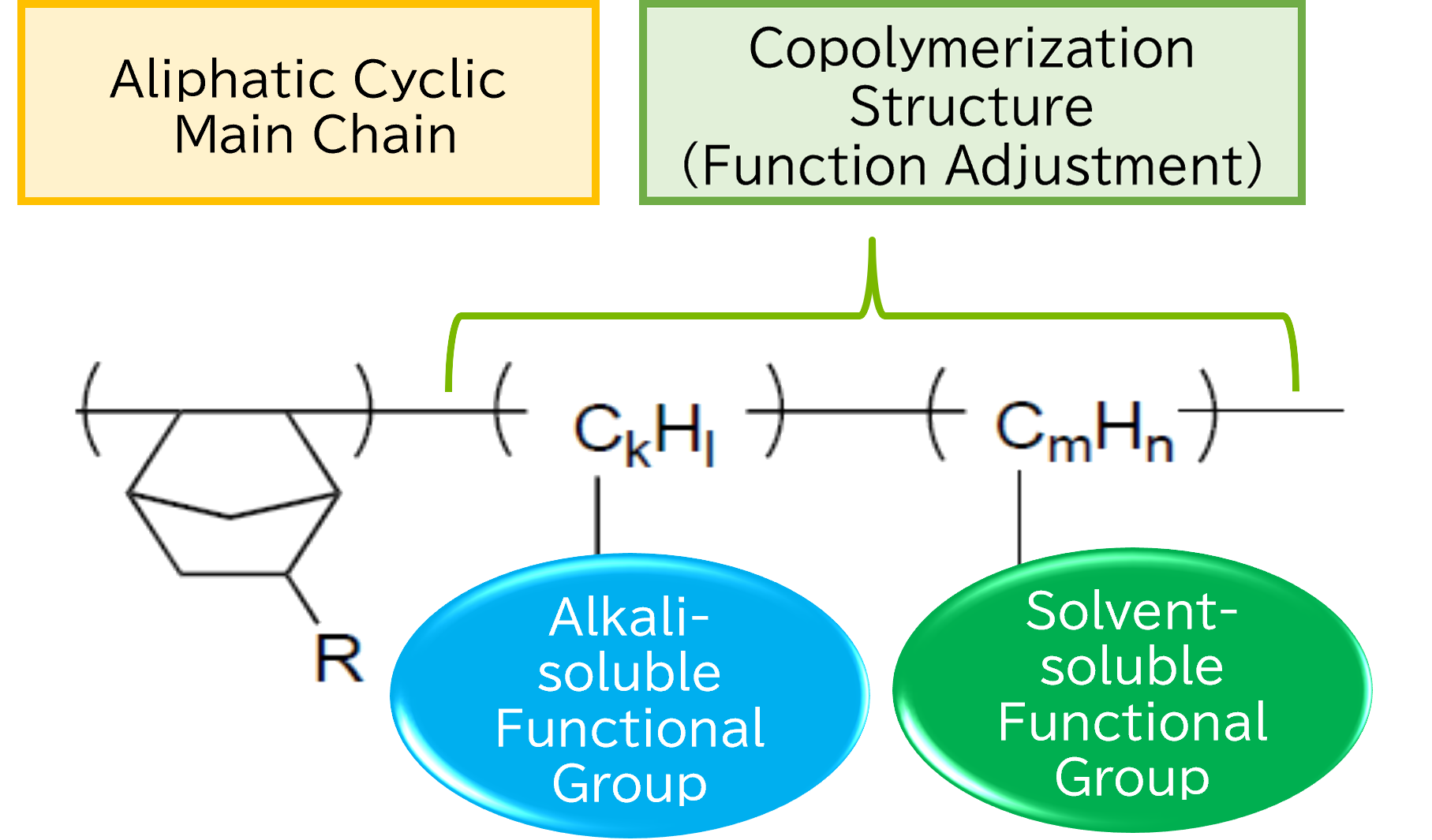
- • High Transparency
- • Low Dielectric
- • Heat Resistant flow
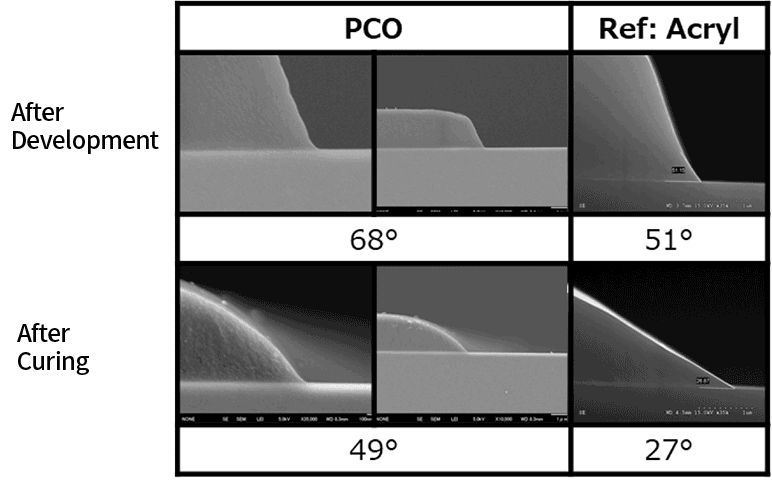
By designing the types of functional groups on the side chains according to the intended application, the desired functionalities can be achieved. By introducing suitable functional groups for resist applications, it becomes possible to apply them as positive or negative-tone patterning materials that can be developed with alkaline solutions.
Item | Condition | Data |
---|---|---|
Sensitivity | mJ/cm2 | 580 |
Residual Film ratio | % (after curing) | 88 |
Light Transmittance (%T) | After curing λ=400nm | 92% |
Dielectric Constant | 100kHz | 2.9 |
Thermal Stability | TGA 250° 60min | 1.3 |
Water Absorption | RT H2O immersion | 0.7% |
(Measurement conditions) Substrate: Glass, FT: 2.5μm, PAB:100°C, 120sec, Exposure: GH line stepper Dev.: 2.38%TMAH, 90sec, 23°C, Cure: 230°C, 30min |
Note
- The values listed in the catalog are representative values.
Example of use according to application (2)
Negative Photoresist
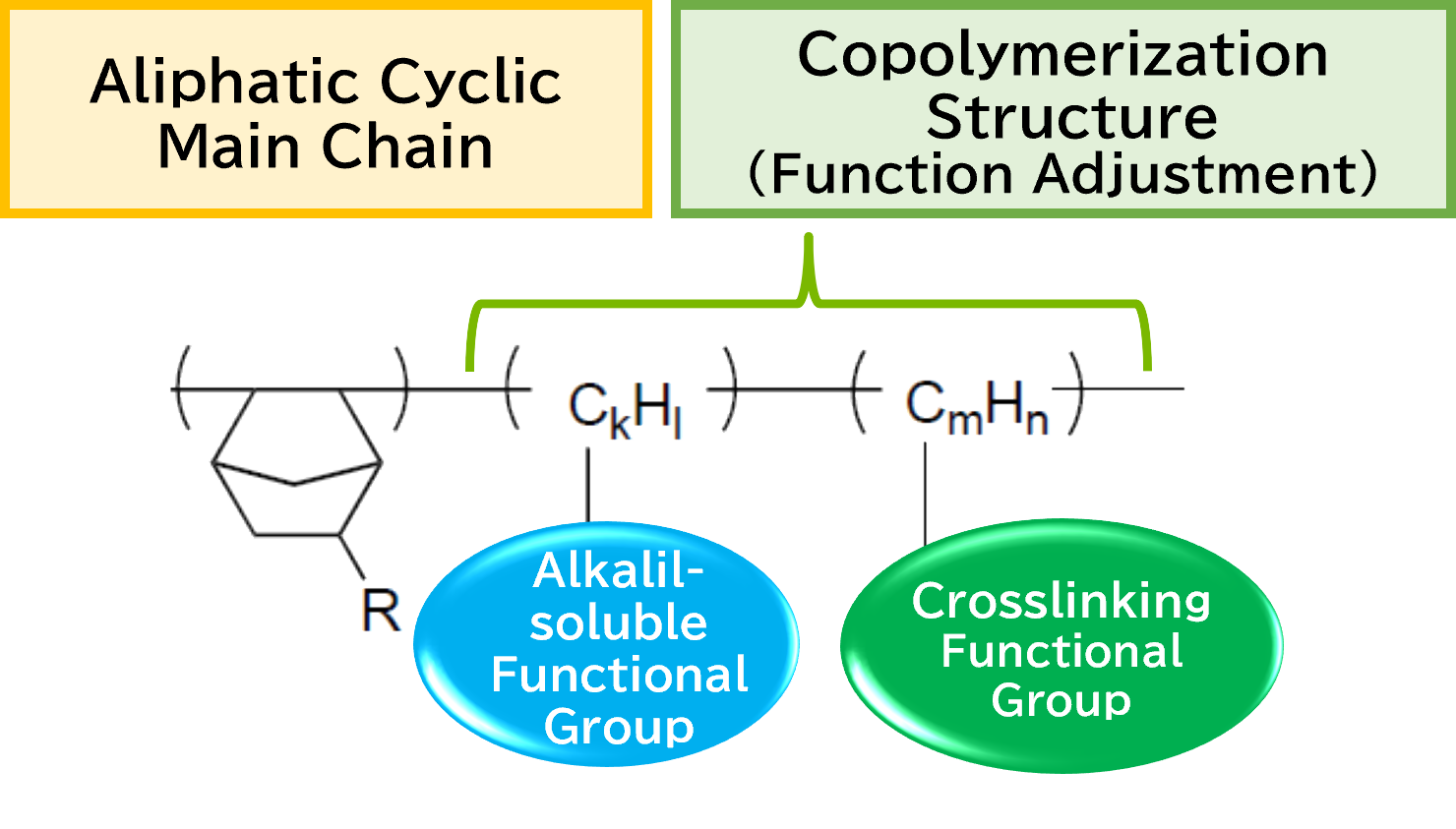
- • Photocrosslinkability
- • High Transparency
- • High Heat Resistance
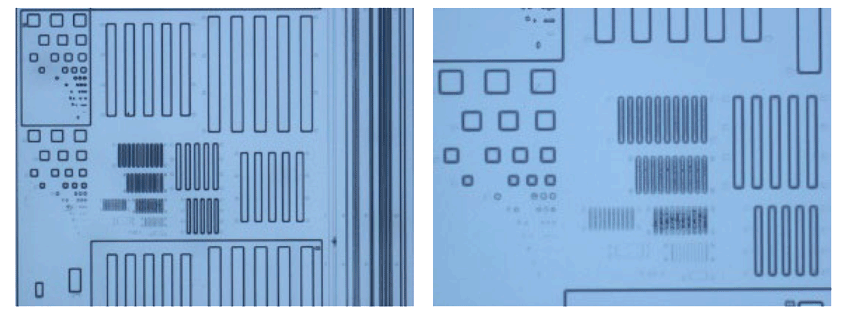
Through exposure to UV light via a mask, it is also possible to apply photocrosslinking curing reactions. After exposure, development with alkaline solutions can be performed to achieve negative pattern formation.
It can be used as a negative photoresist for applications such as semiconductors and displays, exhibiting effective functionality as a negative resist. By incorporating alkali-soluble and crosslinkable functional groups, it functions as a resin for negative-type resist.
Through exposure to UV light via a mask, it is also possible to apply photocrosslinking curing reactions. After exposure, development with alkaline solutions can be performed to achieve negative pattern formation.
Item | Condition | data |
---|---|---|
Remaining Film Ratio (after curing) | 230°C, 60min in Air | 84% |
Light Transmittance | 230°C, 60min λ=400nm | 89% |
TGA | Td5, degC | 309 |
(Measurement conditions) |
Note
- The values listed in the catalog are representative values.
Topics More
- 2024/12/26 Products Development of SUMIKON® AM-3800 - a Diallyl Phthalate (DAP) molding compound for high voltage (800V) and high heat resistance
- 2024/10/18 Products SNC Industrial Laminates Sdn. Bhd. (Malaysia) Expansion of Liquid Phenolic Resin Supply
- 2024/10/16 Products Development of Fire Resistance Phenolic Molding Compounds for EV Batteries
- 2024/05/14 Products Development and Sales of Cyclo-Olefin Polymers (COP) to Meet Diverse Needs
- 2024/04/02 Products Completion ceremony of the new plant for phenolic molding compounds at Sumitomo Bakelite (Nantong) Co., Ltd.